Crude Oil Washing (COW) onboard Ships – Explained
Piping System with respect to Crude Oil Washing:
The pipeline and valves incorporated in the crude oil washing system shall be of steel or equivalent material and shall have adequate strength having regard to the pressure it may be subjected and shall be properly jointed and supported.
The crude oil washing system should contain permanent pipeline and shall be independent of the fire main.
The use of flexible hose pipes to connect the crude oil washing machines shall be fitted with flanges and length should not be more than just to connect the machine.
Provision shall be made to prevent the overpressure in the tank washing system. Any relief valve fitted shall discharge the crude oil in the suction side of the pump.
All hydrants fitted need to be blanked by spectacle bank.
All fitting shall be fitted with isolating valve.
No part of the crude oil washing system pass through the machinery space.
The piping system shall be tested to 1.5 times the working pressure once installed on the ship.
The COW line shall be firmly anchored to ship’s structure.
Read More Crude Oil Washing (COW) Procedure & Precautions on Ships
Number of tanks required to be washed at discharge port with respect to Crude Oil Washing:
- 85% of the VERTICAL surface area inside a tank must be covered by the direct impingement of the jet.
- 90% of the HORIZONTAL surface area inside a tank must be covered by the direct impingement of the jet.
- Jet length is governed by the washing pressure & nozzle diameter.
- Jet length should be such as to be effective in fulfilling the requirements of MARPOL.
- Number of machines that can be run simultaneously is given in the COW operations manual.
- Running more than above machines causes a drop in system pressure and thereby washing effectiveness.
- Minimum system pressure to be maintained is given in the COW operations manual.
- Minimum recommended trim during washing given in the COW operations manual.
- The given conditions of the COW operations manual must be complied with for an effective wash.
- Diameter of piping, Number of machines & fluid velocity in the pipe have a relationship that goes into the designing of the system to satisfy MARPOL constructional & operational requirements.
Precaution against discharge of static electricity with respect to Crude Oil Washing:
A mixture of crude oil and water can produce an electrically charged mist during tank cleaning.
For this reason, if oil in a tank used for the load-on-top procedure (usually one of the slop tanks) is used as a source of crude oil washing fluid, it shall be discharged ashore completely and then filled with oil shifted from another tank using a cargo line.
Precautions to be taken while Crude Oil Washing:
- Commencing washing with large accumulations of oil remaining in the tank.
- Adding chemical agents to the tank washing water.
- Recirculating tank washing water.
- Washing large cargo tanks (greater that 10,000 cubic meters).
- Static electricity, or more properly ‘electrostatic charging’ can be produced during tank washing operations by:
- Accumulation of tank washings in the cargo tank. The oil/water mixture will be subject to charge separation and may produce an accumulated electrostatic charge.
- Spraying or splashing of oil. Crude oil washing will produce electrostatic charging in the cargo tank. Water washing of a tank which has not been adequately drained may also cause charge accumulation.
- Use of conductive ullage tapes to measure tank bottoms during tank washing. Permanently installed ullaging equipment should be used to verify correct stripping during tank washing. Wait one hour after tank washing (if artificial ventilation is used), before sounding a washed tank, five hours if only natural ventilation is used. Tanks may be sounded in less time if a natural fibre line and wooden sounding rod are used. No precautions are necessary if sounding inside a metal sounding pipe.
- Floating conductors in the tank. Dropped or lost sample cans which remain afloat in the tank do not accumulate charge, but can produce a path for the short circuit of an accumulated charge from the surface of accumulated tank washings to the tank structure.
- Steaming of cargo tanks. If cargo tanks are steamed using hoses which are not properly bonded to the ship’s piping, an electrostatic charge will accumulate on the hose. The water droplets from the steam will accumulate electrostatic charge and may cause an incendiary spark if the tank is steamed too vigorously. Therefore tanks should be steamed only with fixed apparatus, only at low velocities and only when the tank is free of any grounded probes (including properly bonded tank washing machines).
Crude Oil Washing: Bar diagram:
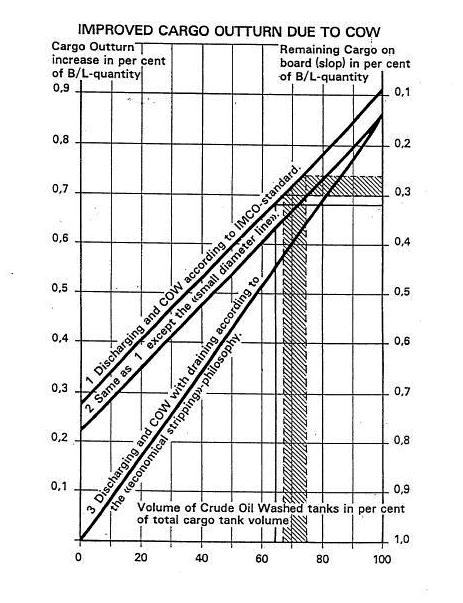
This diagram is based on the commonly recognised estimation that approximately one per cent of Bill of Lading quantity will remain in ship’s cargo tanks after discharging without COW and thorough draining.
Line 3 The “economy stripping” philosophy – quick turnaround in the discharge port more appreciated than spending few hours on stripping to get well drained tanks – was practised and encouraged until the price of crude oil started to rise drastically.
Line 2 Several investigations have shown that a through after-draining with educators have increased the cargo out-turn with 0.2 – 0.5 per cent of the Bill of Lading quantity, and even more in some cases, approximately 500 – 1,250 tonnes for 250,000 tonnes of cargo.
Line 1 Draining (discharging) and COW according to IMO specifications, utilizing the small diameter line, will further improve the cargo out-turn compared to result obtained according to line 2.
COW Manual
Each Crude Oil Washing Operations and Equipment Manual must include the following information:
- The text of the Annex of Resolution 15 of the MARPOL 73/78.
- A line drawing of the tank vessel’s COW system showing the locations of pumps, piping, and COW machines.
- A description of the COW system.
- The procedure for the inspection of the COW system during COW operations.
- Design characteristic information of the COW system that includes the following:
- Pressure and flow of the crude oil pumped to the COW machines.
- Revolutions, number of cycles, and length of cycles of each COW machine.
- Pressure and flow of the stripping suction device.
- Number and location of COW machines operating simultaneously in each cargo tank.
- The design oxygen content of the gas or mixture of gases that is supplied by the inert gas system to each cargo tank.
- The results of the inspections recorded when passing the inspections under § 157.140.
- Characteristics of the COW system recorded during the COW operations when passing the inspections under § 157.140 that includes the following:
- Pressure and flow of the crude oil pumped to the COW machines.
- Revolutions, number of cycles, and length of cycles of each COW machine.
- Pressure and flow of the stripping device.
- Number and location of COW machines operating simultaneously in each cargo tank.
- The oxygen content of the gas or mixture of gases that is supplied by the inert gas system to each cargo tank recorded during COW operations when passing the inspections under § 157.140.
- The volume of water used for water rinsing recorded during COW operations when passing the inspections under § 157.140.
- The trim conditions of the tank vessel recorded during COW operations when passing the inspections under § 157.140.
- The procedure for stripping cargo tanks of crude oil.
- The procedure for draining and stripping the pumps and piping of the COW system, cargo system, and stripping system after each crude oil cargo discharge.
- The procedure for crude oil washing cargo tanks that includes the following:
- The tanks to be crude oil washed to meet § 157.160.
- The order in which those tanks are washed.
- The single-stage or multi-stage method of washing each tank.
- The number of COW machines that operate simultaneously in each tank.
- The duration of the crude oil wash and water rinse.
- The volume of water to be used for water rinse in each tank.
- The procedures and equipment needed to prevent leakage of crude oil from the COW system.
- The procedures and equipment needed if leakage of crude oil from the COW system occurs.
- The procedures for testing and inspecting the COW system for leakage of crude oil before operating the system.
- The procedures and equipment needed to prevent leakage of crude oil from the steam heater under § 157.122(i) to the engine room.
- The number of crew members needed to conduct the following:
- The discharge of cargo.
- The crude oil washing of cargo tanks.
- The simultaneous operations in paragraphs (a)(19) (i) and (ii) of this section.
- A description of the duties of each crew member under paragraph (a)(19) of this section.
- The procedures for ballasting and deballasting cargo tanks.
- The step by step procedure for the inspection of the COW system by vessel personnel before COW operations begin that includes the procedure for inspecting and calibrating each instrument. (Operational Checklist)
- The intervals for on board inspection and maintenance of the COW equipment. Informational references to technical manuals supplied by the manufacturers may be included in this part of the manual.
- A list of crude oils that are not to be used in COW operations.
- The procedure to meet § 157.155(a) (4).
Advantages & Disadvantages of C.O.W.:
CRUDE OIL WASHING:- This section summarise the objectives and prescribes the procedure for the crude oil washing (COW) of cargo tanks, in addition to the Section 6.1.2 of this chapter.
The Master is responsible for monitoring and verifying compliance with this procedure.
Purpose of Crude Oil Washing:-
The objectives of the introduction of the COW system can be said:
- Rationalization of tank cleaning operations.
- Rationalization of cargo work including complete discharge of crude oil; and
- Prevention of marine pollution by minimizing the amount of residual oil retained on board.
- Formation of was coatings and resultant prevention of corrosion inside tank.
Cargo Grade Oil used for Crude Oil Washing:-
- Selecting Oil for COW:- The following points should be taken into account for deciding what grade of oil to use for crude oil washing:
- Mixture of different grades of oil should be avoided.
- Where the tank is washed by a two-stage method, top and bottom, the top wash shall be carried out with the same grade of oil to avoid contamination but a bottom wash with a different grade of oil may be possible if unavoidable, with approval of the cargo consignee.
- If a different grade of oil is used as wash oil with the agreement of the cargo consignee, it will be advantageous to use crude oil with less sediments.
- Check the necessity for flushing with fresh crude oil, and if necessary, such quantity.
Tank to be Crude Oil Washed:- Cargo tanks necessary to be washed are as follows:
- Cargo tanks specified in Section 6.1.2 of the COW Manual.
- During cargo discharge before dry docking.
Regardless of the number of tanks required to be crude oil washed by the MARPOL 73/78 convention, all tanks should be washed by crude oil as far as possible for the purpose of preparation for ballasting and sludge control.
Prohibited Matters Concerning COW:-
- Crude oil washing shall not be carried out during a ballast passage.
- Ballast should not be loaded in tanks which were not crude oil washed.
- Water filled in a tank already crude oil washed but not yet rinsed with water shall be regarded as dirty ballast.
Crude oil Washing at Sea Between Discharge Ports:-
- In any case, crude oil washing shall be finished before departure from the final discharge port.
- In the case of two or more discharge ports, it is possible to carry out crude oil washing at sea between such discharge ports.
- In this case, washed tanks shall be left empty, ready for a dry inspection at the next discharge port, prior to sailing.
- This inspection is to be conducted by sounding several parts of the tank bottom, etc. when the tank is empty.
- Crude oil washing between discharge ports may minimize any potential delays whilst discharging operation
- The same safety and pollution precautions shall be taken as in port.
Method of Crude Oil Washing:-
- Cleaning Methods:-
- Multi-Stage System: While cargo oil is still in a tank, the upper part above the oil surface is washed (top wash) and the bottom is washed (bottom wash) by stripping tank washing after the tank has been emptied.
As one version of this method, when tank washing is divided into two stages, namely top and bottom, it is called a two-stage method.
- Top Wash:-
- The washing area is from the joint section of the upper deck and the bulkhead downward to a height slightly above the oil surface.
- In the case of multi-stage system, each stage should be overlapped.
- In general, sludge accumulates on the horizontal girders, the top wash therefore should be started when the oil level reaches about three (3) metres above the bottom unless specified in vessel’s COW operation Manual.
- The top wash terminates when the remaining oil level goes down to about 1.5 metres above the bottom.
- Crude oil used as a medium for washing should, in principle, be the same grade of oil as the one being discharged to prevent contamination.
- Bottom Wash:-
- This operation starts when cargo oil has been discharged and roughly stripped from the bottom to become dry, and the bottom which has been left unwashed at the time of the top wash is washed as many times as necessary.
- In general, the nearer to the bottom, the more sludge deposits, and the bottom wash should be carried out with more care as compared with the top wash.
- Spot Washing and Repeated Washing: Some of the single nozzle type of machine developed for crude oil washing are capable of repeated washing or spot washing of a particular are by horizontal as well as vertical angle control.
- Single – Stage System:- This is a method combining the Top and Bottom washes together as a continued process. When a tank empties, the entire tank walls are washed altogether but the method itself is not practically different from conventional seawater washing.
The following are considered to be the prerequisites for this washing:
- The tank shall be empty before washing.
- The number of machines should be well balanced with the stripping capacity.
- Washing Oil Supplying Systems: – There are basically three wash oil supplying methods so called “Open Cycle”, “Closed Cycle” or “Bleed-off System” as mentioned below:
- Semi-open Cycle System:-
- Wash oil is introduced from a tank being discharged and drained oil is discharged into the aftermost centre tank or slop tank.
- Precaution:- The tank be used as a source of crude oil washing (Driving Oil) should be first discharged at least one metre in depth before supplying as a washing medium to suppress electrostatic charges.
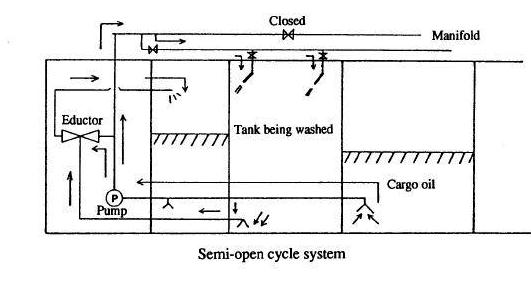
- Closed Cycle System (Re-Circulation method):-
- Wash oil is supplied from the aftermost centre tank or slop tank and drained oil is collected in the same tank, i.e., the same tank is used for both purposes.
- Precaution:-
- Slop tanks loaded by the “Load-on-Top” procedure should be discharged entirely and then filled with fresh oil (crude oil free from water and residue) prior to COW.
- It is considered better to discharge Driving Oil in Slop tank after washing a few tanks, not more than six tanks, and replace to fresh oil again as it may avoid the Driving oil to be sludge-full.

Bleed-off System (Open Cycle System):- A method in which a part of the oil being discharged is branched off to the tank cleaning line. Some terminals call this system in which cargo is discharged simultaneously with COW, “open cycle”.
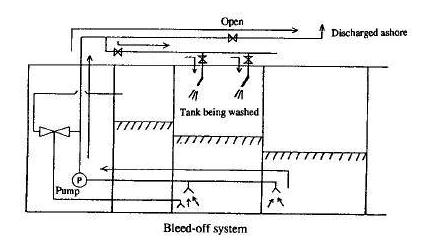
Application to Crude Oil Wash:- If COW is planned to take place at a Japanese discharge port, the application for COW shall be submitted to the local agent for permission, with a copy to the Company.
Advantages with COW:-
Providing that equipment and procedures are well adapted for COW, the following advantages are gained in comparison with water washing:
- Considerable reduction in pollution potential since less oil remains on board after discharge and less oil-contaminated water is handed during the ballast passage.
- Reductions in time and cost of tank cleaning.
- De-sludging by hand obviated.
- Reduced tank cleaning time at sea.
- Increased out-turn of cargo.
- Reduced dead freight as less oil-water slops are retained on board.
- Less salt water discharged to refineries.
- Tank corrosion due to water washing is reduced.
- More time for maintenance work at sea, since no additional tank cleaning is required, except water rinsing of tanks to contain arrival ballast.
Disadvantages with COW:-
- Increased workload during discharging.
- Prolonged time for discharging.
- Costs for extra personnel.
- Costs for COW equipment
- Potential safety and pollution risks.
- More equipment – higher demand for maintenance.
Therefore, it is important to plan the discharge operation properly so that COW is not interfere with in any way, increase of discharge time will be least when cargo discharge is restricted by shore limitations.
Requirements of Crude Oil Washing (COW) on oil tanker as per MARPOL 73/78 Convention:
- Crude oil tankers of 20000 dwt and above delivered after June 1, 1982 as defined in MARPOL 73/78 convention are to be equipped with cargo oil tank washing systems by using crude oil washing.
- The equipments and arrangements of crude oil washing apparatus and associated equipment should comply with the requirements of “Specifications for the Design, Operation and Control of Crude Oil Washing Systems” which adopted by IMO.
- The “Specifications for the Design, Operation and Control of Crude Oil Washing Systems (resolution A.446 (XI)” has been adopted by IMO on 15 November 1979.
- The amendment of Resolution A.446 (XI), as amended by A.497 (XII) has been adopted by IMO on 19 November 1981.
- The amendment A.897 (21) of Resolution A.446 (XI), as amended by Resolution A.497 (II) has been adopted by IMO on 25 November 1999.
- Every oil tanker operating with crude oil washing systems is to be provided with an Operations and Equipment Manual detailing the system and equipment and specifying operational procedures.
- Such a Manual is to be in standard format in the Appendix of Resolution MEPC.3(XII) as amended by MEPC.81(43).
- If the Manual is not compiled in English or French, the text is to include a translation into one of these languages.
Crude Oil Washing: Cargo grades not suitable for COW
COW work using condensate oil that includes crude oil of high vapor pressure should not be performed.
If COW of the said tank is necessary, then washing with a different grade of oil should be considered. (If washing with crude oil of high vapor pressure is unavoidable, permission of the terminal should be obtained. Also, when washing with a different grade of oil, the permission of the charterer should be obtained.)
Hazards associated with Crude Oil Washing:
- Oil leaks: – Oil leaks are always dangerous since COW work is performed at high pressure of about 1.0 mPa (about 10 kg/cm2).
- The COW line is installed until near the bow on the exposed deck and is subject to severe environmental conditions. The line installed to the COW machine has several connections and a large number of locations need to be inspected. Even if an adequate number of tests are carried out when the ship is underway and no abnormalities have been found, conditions during the discharging operation vary, and safety cannot be guaranteed based on the tests alone.
- Risk of explosion: If oxygen content is higher, there is always chance of explosion due to the formation of static charges.
- Risks of cargo contamination.
- Risk of overflow.
- Air pollution.
Checklist Before Crude Oil Wash Operation:
- Are all pre-arrival checks and conditions in order?
- Has discharge/crude oil washing operation been discussed with both ship and shore staff and is agreed plan readily available for easy reference?
- Has communication link between deck/control station and control station/shore been set up and is it working properly?
- Have crude oil wash abort condition and procedures been discussed and agreed to by both ship and shore staff?
- Have fixed and portable oxygen ana
- lysers been checked and are they working properly?
- Is the inert gas system working properly and is the oxygen content of inert gas being delivered below 5 percent by volume?
- Is oxygen content of tank(s) to be crude oil washed below 8 percent by volume?
- Have all cargo tanks positive inert gas pressure?
- Has a responsible person been assigned to check all deck lines for leaks as soon as washing starts?
- Are the fixed machines set for the required washing method and are portable drive units, if fitted, mounted and set?
- Have valves and lines both in pump room and on deck been checked?
Checklist During Crude Oil Washing Operation:
- Is the quality of inert gas being delivered frequently checked and recorded?
- Are all deck lines and machines being frequently checked for leaks?
- Is the crude oil washing in progress in designated cargo tanks only?
- Is the pressure in the tank wash line as specified in the Manual?
- Are cycle times of tank washing machines as specified in the Manual?
- Are the washing machines in operation, together with their drive units if applicable, frequently checked and are they working properly?
- Is a responsible person stationed continuously on deck?
- Will trim be satisfactory when bottom washing is in progress as specified in this Manual?
- Will the recommended tank draining method be followed?
- Have ullage gauge floats been raised and housed in tanks that are being crude oil washed?
- Is level in holding tank for tank washings frequently checked to prevent any possibility of an overflow?
Checklist After Crude Oil Washing Operation:
- Are all valves between discharge line and tank wash line closed?
- Has tank wash line been drained of crude oil?
- Are all valves to washing machines closed?
- Are cargo pumps, tanks and pipelines properly drained as specified in the Manual?
It is very important to drain the crude oil washing lines as soon as possible after completing washing. This gives the oil time to run dry before the discharge is terminated by use of the stripping pump through the small diameter line.
The preceding lists are recommended by IMO regarding content. The ship, company and local authorities may also have additions to the content. Also remember to record the crude oil washing operation in the “cow-log”.
Proper Sequence Procedures to be followed for unloading of cargo and COW in an Oil Tanker:
- Prior arriving at the discharge port an exchange of information between the ship and the terminal will take place.
- Once the vessel is tied up at the terminal, a ship-shore checklist will have to be filled out.
- The general safety checks and precautions will be the same as given for the loadport.
- Since pumps will be running at the discharge port, special attention will have to be given to monitor the safe running of the pumps.
- Pumproom ventilation should be running throughout operations. Proper pumproom entry procedures should be followed.
- All crew should be aware of the fire and safety equipment available in the pumproom. Drips and leaks in the pumproom should be attended to immediately. Pumproom bilge soundings should be monitored regularly.
- After completion of gauging/sampling and calculation the terminal will give indicate readiness for receiving the cargo.
- The chief officer will line up for discharge. Ideally cargo will be started by discharge from a single tank.
- In steam turbine cargo pumps it is important to warm up the pump gently.
- RPM of the pump will be slowly increased after all checks have been made. Inert gas will replace the volume of cargo discharged. The maximum oxygen content of the IG from the IG plant should be 5% and the tank should have a maximum of 8%.
- The IG pressure should be monitored very carefully to avoid over or under pressurizing of tanks.
- When all checks have been completed, it will be safe to proceed to open up more tanks and start more pumps. Discharge pressure at the manifold to be monitored periodically.
- The next important stage comes when a tank is nearing empty levels. When some oil is still left in the tank, the rpm of the pump should be reduced.
- Changeover procedure from one tank to another should be gradual.
- The valve of the tank nearing empty should be slowly throttled while the pump is fed by another tank which has a higher level of oil. Using the vac-strip pump or in its absence the stripping pump will be vital to avoid the pump misbehaving.
- In case a pump loses suction at any time, the rpm will increase dramatically. The pump should be stopped immediately in such a case or immediate measures should be taken to supply cargo oil to the suction side of the pump.
- The use of a bar chart and thorough planning are the key points of an efficient discharge. Ballast should be taken into the ballast tanks as per the ballast plan worked out before arrival.
- COW operations will also be required and this is dealt with later. IG should be vented, if necessary, through the mast riser or sent ashore through the vapour recovery system, if fitted. Judicious planning will ensure that the amount of IG vented to the atmosphere is restricted to the bare minimum. (Notes on COW operation mentioned before)
- During the tail end of the discharge it may be necessary to employ the educator/ stripping pump to drain the last remnants of the cargo into the slop tank.
- The last tank to discharged will be the slop tank. Finally, after completion of discharge from the tanks, it will be necessary to drain and strip all the lines. Discharge of the final line stripping should always be done through the small diameter line (MARPOL line).
Open Cycle and Closed cycle tank washing in a crude oil tanker:
Open cycle Washing:- This is the method of taking washing oil from tanks other than the washing tank and slop tank for washing, and transferring the stripped oil to the slop tank. In AUS-equipped ships, the method of directly discharging the directly-stripped oil is used rather than transferring it to the slop tank.
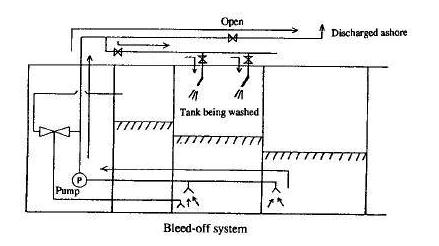
Advantage:- The washing capacity and the tank draining capacity is such that the level in the tank to be washed and the slop tank will not rise so it is safe.
Disadvantage:- It is very time consuming.
Closed Cycle Washing:- This is the method of taking washing oil from the slop tank for washing and returning the stripped oil to the slop tank using the stripping machine.
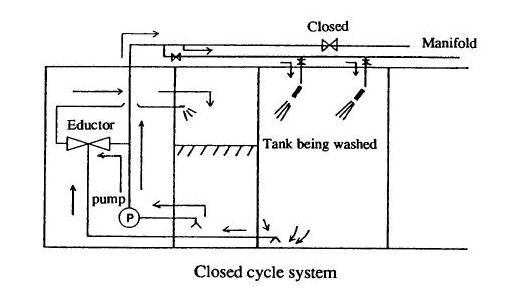
Advantage:- It is less time consuming.
Disadvantage:- The wash water cannot be directly transferred ashore and the water / oil level in the tank keeps on rising so there are chances of overflow.
Read More Crude Oil Washing (COW) Procedure & Precautions on Ships